Por Marcondes Silvestre Takeda*
O acréscimo acelerado da quantidade e da utilização de aparelhos elétricos em todos os principais setores da economia tem levado ao respectivo aumento no consumo de energia, o que, por consequência, afeta o meio ambiente.
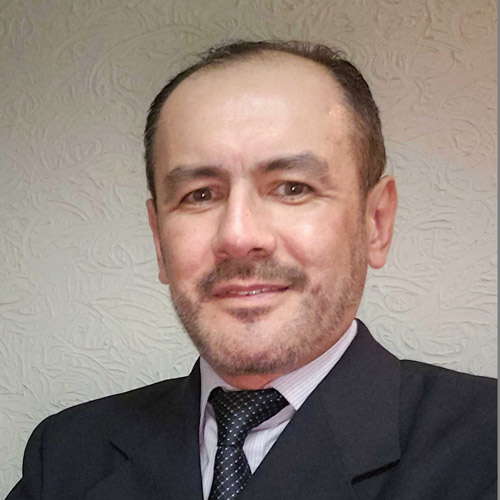
Neste cenário, o uso mais eficiente de energia é essencial em um processo de desenvolvimento sustentável. Tecnicamente falando, a eficiência energética consiste na relação entre a quantidade de energia empregada em uma atividade e aquela disponibilizada para sua realização.
Em outras palavras a eficiência energética é a utilização racional de energia através da redução do seu consumo, mantendo-se os mesmos serviços, sem reduzir o conforto e a qualidade de vida, protegendo o meio ambiente e garantindo o suprimento com um comportamento sustentável em seu uso.
A eficiência energética é uma das maneiras mais fáceis e econômicas de combater as mudanças climáticas, limpar o ar que respiramos, melhorar a competitividade de nossos negócios e reduzir os custos com energia para os consumidores. Podemos até mesmo considerá-la como a “fonte de energia” mais barata a ser explorada!
Compreendemos, então, a razão da eficiência energética ser um dos 10 compromissos básicos do Protocolo de Kyoto (criado em 1997 e em vigor desde 2005) para os países signatários alcançarem a meta de redução dos gases poluentes.
Apesar disso, globalmente, dois terços do potencial econômico da eficiência energética permanecem inexplorados. Segundo a Agência Internacional de Energia (IEA), 70% do uso da energia elétrica no mundo ocorre fora de quaisquer requisitos de desempenho de eficiência.
Em um período de três anos, 2014 a 2016, o desperdício de energia custou ao Brasil R$ 61,7 bilhões, de acordo com o levantamento da Associação Brasileira das Empresas de Serviços de Conservação de Energia (ABESCO).
Globalmente, a indústria é de longe, a maior consumidora de energia elétrica sendo no Brasil responsável por 41% do total. Ainda em nosso país, segundo a publicação “Bloco Especial sobre Indústria e Energia da Sondagem Empresarial” realizada pela Confederação Nacional da Indústria (CNI) em 2015, o insumo energia elétrica é estratégico, utilizado por 79% das empresas e podendo representar mais de 40% de seus custos de produção.
Logicamente, sendo um dos principais insumos dessa cadeia, é fundamental a sua utilização de maneira racional e econômica tanto quanto possível. Esta relevância é ainda maior nas chamadas indústrias eletrointensivas: alimentícia, celulose e papel, química básica, refino de petróleo, siderúrgica, metais não ferrosos (principalmente alumínio) e minerais não metálicos (principalmente cimento).
Na indústria, as perdas de energia on-site, isto é, a energia perdida no sistema devido as ineficiências de equipamentos, limitações operacionais termodinâmicas, distribuição de energia na planta e na conversão de energia em trabalho útil, representam alvos imediatos para melhorias na eficiência energética.
De acordo com um estudo da “Energy Information Administration (EIA)” dos Estados Unidos, em média 22% da energia é perdida dentro dos limites da planta industrial antes de chegar ao processo. Da energia efetivamente entregue ao processo, de 20% a 50% também pode ser perdida nas formas de desperdício em calor, queimas e subprodutos entre outras.
Em geral, as perdas podem ser reduzidas com a adoção de tecnologias mais eficientes, melhor integração entre dissipadores de calor e fontes dentro da planta, aumento da utilização da energia não aproveitada e melhores práticas de operação e manutenção.
A redução de perdas on-site tem um duplo efeito, uma vez que será necessário menos energia a ser produzida pela fonte primária, principalmente nas indústrias eletrointensivas.
A última “Pesquisa de Posse e Hábitos de Uso de Equipamentos Elétricos – PPH” da Eletrobrás/Procel mostrou que a força motriz é responsável por 68,3% do consumo de energia elétrica na indústria.
De acordo com a EIA, aproximadamente metade da eletricidade usada globalmente é consumida em sistemas de motores elétricos. O setor industrial responde por mais de 60% do consumo de eletricidade dos motores em todo o mundo, sendo o restante consumido no setor comercial, agricultura e transporte. Globalmente, a demanda total por uso de energia em motores industriais mais que duplicará até 2040, sendo a China e a Índia responsáveis pela metade deste aumento.
É importante comentarmos que uma significativa parte do parque industrial possui máquinas com mais de duas décadas de funcionamento, projetadas antes das novas tecnologias de gestão de energia.
O maior potencial de economia de energia nos sistemas com motores elétricos geralmente não está no próprio motor, mas sim nas outras partes do sistema. Normalmente o que se percebe é um entendimento limitado sobre o custo da melhoria da eficiência e o potencial de economia de energia.
O motor é apenas um dos componentes do sistema de força motriz, sendo que as melhorias nos demais componentes deste sistema e/ou inclusão de novos dispositivos é que efetivamente serão responsáveis por até 90% do resultado a ser obtido em eficiência energética.
Além da substituição de motores antigos por motores novos de alto rendimento, para melhorar a eficiência operacional do sistema de força motriz, o usuário pode também adotar o inversor de frequência (VFD – Variable Frequency Drive).
É possível conectá-lo ao sistema através de cabos elétricos especialmente projetados para as condições de operação dos VFDs, ou seja, cabos que contribuem com a manutenção da vida útil do sistema. Com a utilização do VFD é possível reduzir o consumo de energia elétrica no sistema de força motriz em pelo menos 30%.
Por fim, logicamente, não poderíamos deixar de dizer que motores de alto rendimento, mais eficientes e compatíveis com dispositivos de melhoria de controle e eficiência estão disponíveis no mercado.
* Marcondes Silvestre Takeda é gerente de produto do Grupo Prysmian no Brasil